Integral Knives - The Hidden Strength Within
Recently I’ve posted a few pictures of the Chute Knife, and I had a few people ask me, “What is so special about the Chute knife?” This is a good question. Our Chute knife, the Integral Hunter, and the famous A.G. Russell Sting are built as Integral knives. First, let me explain what Drop Forging is, and then I’ll explain more about Integral knives.
There are three ways to shape metal tools:
-
Forging - The most basic form of forging is a blacksmith beating a piece of metal in the shape desired.
-
Casting - This involves heating the metal up until it is in its liquid form, and pouring that liquid into a cast. This shapes the metal to the cast. Casting isn’t typically used for knives however.
-
Stock Removal / Machining - This is when you cut away material from a block until it is the shape you want it to be.
Next let me explain what dies are. A die is hardened steel that contains the shape of the finished product you want to make. You can think of it like a mold or a cast.
Types of forging:
-
Drop Forging - hammers heated steel into dies. This is what we use for the Chute Knife, the Integral Hunter, and the Sting Knives.
-
Cold Forging - This is for smaller pieces, and involves forcing metal into the die without heating it significantly ahead of time.
-
Press Forging - Instead of using a hammer, a hydraulic press forces the metal into the die.
-
Roll Forging - This is when hot metal is pressed between two rollers. Roll forging is how Cored Damascus is made. Cored Damascus is when you have Damascus layers on each side of the blade, but a main core steel is the dominant center steel. You can see this on the Power Ball.
Thin sheets of Damascus steel are roll forged on each side of the core steel.
*Roll Forging is of course only the last part of the process for Cored Damascus, the Damascus sheets on each side of the core do have to be forged into the Damascus pattern beforehand.
Integral Knife Construction
The word Integral can mean two things in the knife world. It can refer to the Integral locking mechanism (lumping liner and frame locks together). Or it can refer to the construction of fixed blades. For this article I’m going to focus on the latter.
An Integral fixed blade is one made of all one billet of steel. This means that the blade, bolsters, tang, and pommel are all made out of one single piece of steel. The advantage of this is that the steel grain runs uninterrupted across the entire knife, rather than having multiple steels attached to the main blade. This significantly improves the strength, durability, and lifetime of the blade.
*Note - Not all makers consider the term Integral to also refer to the butt. Some may call their knife Integral but not include the butt in that definition. To be complete, you could refer to a knife made with all one piece (including the butt) to be a Full Integral knife. We just refer to it as simply Integral.
The Chute Knife, the Integral Hunter, and the Sting Knife are Integral knives and are very strong because of it.
Some of you might be thinking “... By that definition I thought ALL knives were Integral.” It CAN be difficult to tell the difference between a well made integral knife and a regular knife. Most knives with a bolster and/or pommel are not made out of the same piece of steel. The majority of bolsters and pommels are added onto the blade through riveting, soldering, or welding.
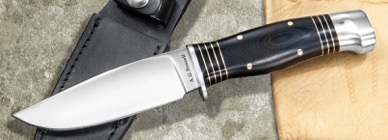
The majority of kitchen knives with metal bolsters on either side of the blade have been welded on. Many times it is of a different steel than the main blade. This isn’t necessarily a bad thing, and doesn’t make your knife weak. Our own Classic American Hunter uses a tough, lightweight aircraft alloy in the guard and butt. This makes the knife extremely lightweight and significantly reduces hand fatigue. You can see the tang reaches to the butt and the alloy is riveted (the small discolored circle in the butt pictured).
But knives that have to stand up to some extreme abuse for field craft or combat benefit from the added strength of being integral. Which is why we chose to make the Sting and the Chute knife as Integral knives.
Does the process of Forging make the blade stronger than machining?
This is a can be a touchy question. The answer is: sometimes. If you are using an old spring from a car to make a knife, then forging is a very important part of aligning the steel grain pattern and hammering out any defects in the steel.
If you are using steel that was designed, treated, and worked to be made into knives, than the differences are minimal to none. The steel manufacturer has already aligned the grain pattern. Machining will only cause minor stress fractures if the object being machined is very complicated - but this isn’t the case with fixed blades, they aren’t that complicated in structure.
In short, forging is very important to the hand makers who are making knives from scratch materials, but not as important to makers and manufacturers who are buying large premade billets of steel ready for machining.
Why do manufacturers use drop forging at all then?
The simple answer is economics. Almost two thirds of the billet will go to waste if you machine a blade out of it. Since you are making a blade out of a high quality steel, wasting two thirds of it gets very expensive.
Dietmar Kressler is one of the few makers who machines integral blades out of a billet. No one can argue with his results, the blades are magnificent! The last of the Chute knives he made for us sold for $2,400. It was a fantastic blade made out of RWL-34. For those who can’t afford high end handmade prices but still want the strength Integral gives, drop forging is the answer.
![]() |
Steel Tidbit: RWL-34 is a version of 154CM made for R.W. Loveless. It is very similar to 154CM, with only a slight variation in the steel composition. It was said to be purer than 154CM and was highly coveted. Take a look at our Steel Chart to see the details.
Why are Drop Forged Knives more expensive?
The answer is that all full Integral knives are expensive to make. Making Integral knives using machining (cutting away the material) is incredibly expensive. Even though Drop Forging isn't as expensive as full machining, proper Drop Forging is still relatively expensive, and requires expensive dies that have limited lifespans before needing to be remade.
These dies must be thick and strong enough to receive hammering blows without warping or breaking. You are basically making a mini anvil shaped as a knife, and only usable for that particular knife. Furthermore, typically there is a die at the top of the hammer, as well as the bottom of the hammer. These dies must stand up to significant pounding under a lot of pressure. All this causes a lot of wear and tear on the dies.
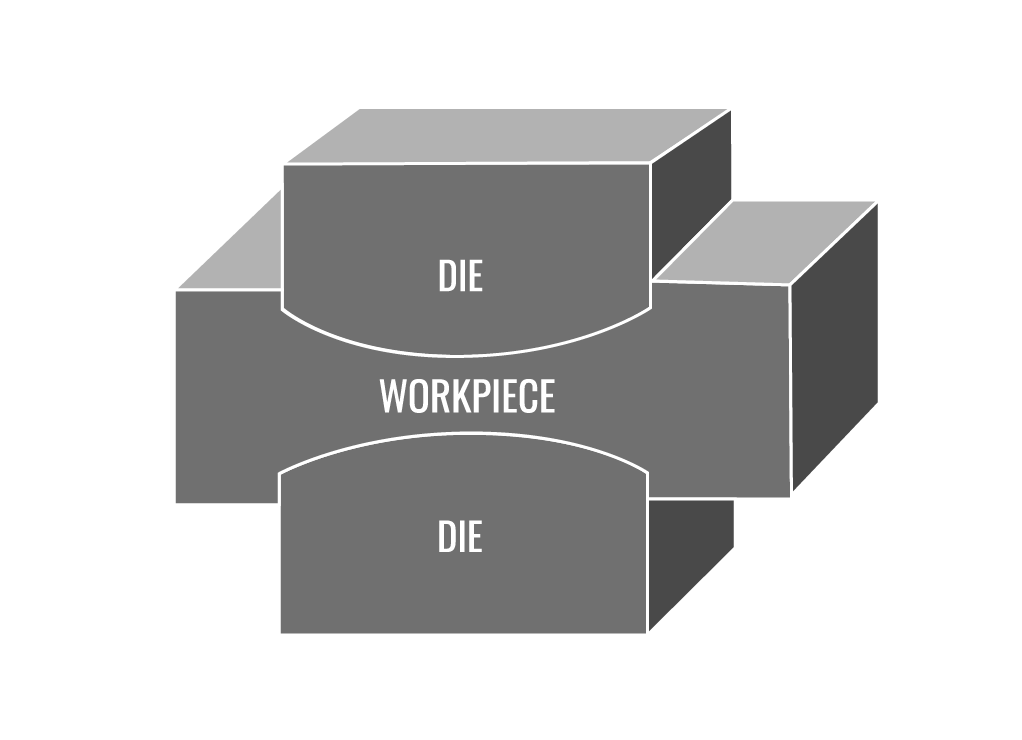
Drop Forging requires a level of professional precision to ensure everything lines up perfectly, and there are no errors. We needed precision work from professionals who were willing to do it our way, rather than the easy way. Our standards of quality are very high. It took us ten years to find a manufacturer who was willing to do drop forging and to make the dies and other tooling required to make the blades.
Taiwanese Made Knives
The Sting 3, the Integral Hunter, and the A.G. Russell Chute knife are Drop Forged, and then hand finished to a beautiful polish, just shy of mirror polished. This is all done in Taiwan. This detailed polish work will help the steel be further resistant to rusts or stains (as opposed to sandblasted). For some models we add our own handle materials and a few touch ups at our shop here in Rogers, AR.
Taiwan makes some excellent, high quality knives. Taiwan’s manufacturing for the knife industry has grown significantly over the last several decades, as has their efficiency and skilled workmanship. Ourselves (A.G. Russell Knives), a couple Benchmade, Browning, Buck, Boker, most of the CRKT knives, Gerber, KA-BAR, SOG, Spyderco, Timberline, Outdoor Edge, Ontario Knife Company, and many other knife companies all are producing or have had knives produced in Taiwan at one point or another. These are all well known knife companies, most (if not all) with excellent reputations and well known for producing top notch, quality knives.
Certainly many companies use Taiwan to produce the lower end budget blades for the average Joe who can’t afford a higher quality knife. However even these budget blades have a fair quality to them (the quality of some of the CRKT and Kershaw budget blades is astounding for the price).
Despite being known for budget blades, Taiwan is capable of far more. Have you seen some of the high end multi-hundred dollar blades Spyderco is producing in Taiwan?
![]() |
While Spyderco’s aesthetics aren’t my favorite, you can’t argue with the quality construction they come out with. Spyderco has a U.S. plant which does excellent work, but if you look at Spyderco’s offerings, most of their higher end knives come from Taiwan.
I produced the original Sting and Sting 2 in Germany. Since we are a small company, the majority of our knives are made in batches, rather than continuously. We ran out of the Sting 2, and I found that the originals were going for over $300 on the secondary market. $300 is a lot of money, a week’s wages for some.
I wanted to make the Sting more affordable. I needed to find a new manufacturer to make my design for the Sting 3. I got quotes from Germany and Taiwan. The German quote for tooling and the price per knife was staggering. The Taiwanese offer allowed me to lower the price on the Sting 3 significantly for my customers, and more importantly, the samples made in Taiwan were of a higher quality than what I received from Germany. After a little back and forth perfecting how it was being made, we came out with the Sting 3. I am very pleased with it. It turned out beautifully.
Summary
The Sting 3, the Integral Hunter, and the A.G. Russell Chute knife are beautiful, strong, tough Integral blades. They are drop forged because it is most logical and economical means of production of tough Integral blades, and their intended use warranted the extra strength provided by being Integral. This process is unfortunately a bit more expensive than other methods, but in my opinion worthwhile. In short - you get what you pay for.
Thanks for reading!